In the realm of industrial manufacturing, the efficiency and environmental impact of cleaning processes are paramount. Traditionally, steam cleaning has been the method of choice due to its effectiveness and simplicity. However, as environmental regulations tighten and sustainability becomes more crucial, there is a growing need to explore alternative cleaning methods that are both effective and have a lower environmental footprint. This paper aims to evaluate the transition from steam cleaning to alternative methods such as chemical and hot water cleaning, assessing their technical feasibility, environmental implications, and economic considerations.
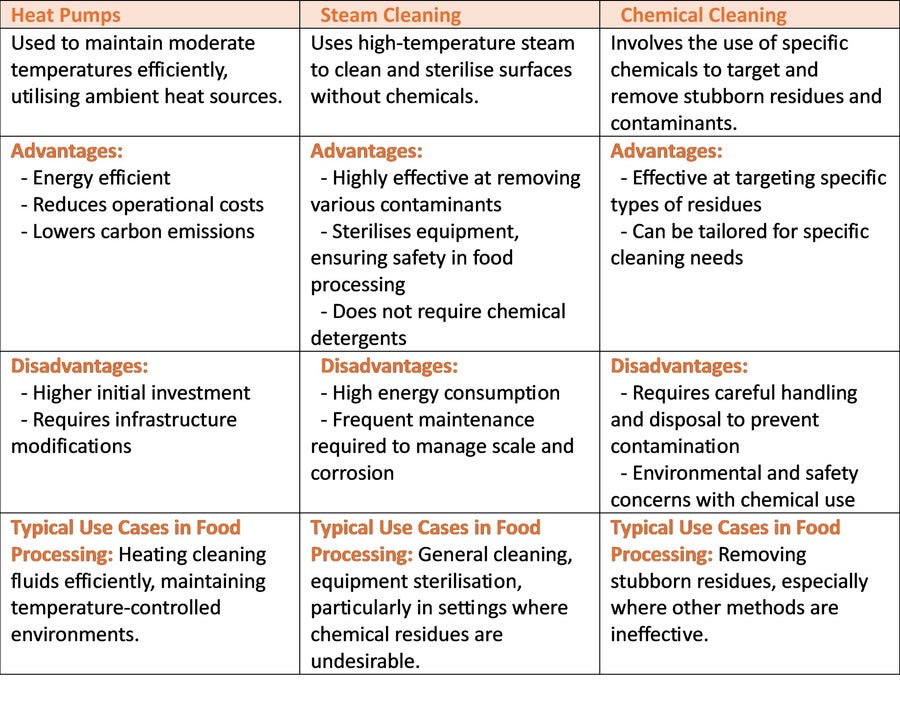
Current State: Steam Cleaning
Steam cleaning utilises high-pressure steam for the removal of dirt, grease, and other contaminants from surfaces and equipment in manufacturing settings. This method's primary advantage is its ability to sanitise without the use of harsh chemicals, which is achieved by the heat of the steam alone. Steam boilers, which are integral to this process, typically operate with an efficiency of 70% to 80%, with newer models reaching up to 90%. Despite its effectiveness, steam cleaning requires substantial energy input, predominantly from natural gas, contributing to significant carbon emissions and operational costs.
Steam systems also face challenges such as scale build up, which reduces efficiency over time, and the need for continuous maintenance to manage corrosion and wear. Additionally, the elevated temperatures and pressures involved pose safety risks, necessitating strict compliance with health and safety regulations.
Alternatives to Steam Cleaning
There are alternatives that can be reviewed regarding steam clean which could be:
• Chemical Cleaning
• Hot Water Cleaning
Chemical Cleaning
Chemical cleaning in industrial settings involves the use of various chemical solutions to remove residues that are difficult to clean with water alone. This method is particularly effective against specific contaminants such as heavy oils, biological films, and mineral deposits. Chemicals used can range from mild detergents to strong acids and alkaline solutions, depending on the nature of the contaminants and the surfaces being cleaned.
The primary advantage of chemical cleaning is its ability to target specific types of dirt and residue efficiently. However, the use of harsh chemicals raises concerns regarding worker safety, environmental impact, and the need for proper disposal mechanisms. Regulations often dictate stringent handling and disposal procedures to mitigate these risks. Furthermore, the environmental footprint of producing and disposing of these chemicals can be significant, necessitating careful consideration and planning.
Hot Water Cleaning
Hot water cleaning uses water heated to an elevated temperature but below boiling point to remove dirt and grease. This method combines the mechanical action of water with elevated temperatures to enhance cleaning effectiveness without the risks associated with high-pressure steam.
Hot water systems are typically less energy-intensive than steam systems and can be integrated with energy-efficient technologies such as heat pumps, which can significantly reduce their environmental impact. The primary challenge with hot water cleaning is ensuring that the water temperature is sufficient to achieve the desired cleaning effectiveness without the supplemental use of chemicals, which may still be necessary for certain residues.
Temperature Requirements
Both alternative methods must meet specific temperature criteria to be effective. Chemical cleaning may operate at various temperatures based on the chemical properties, while hot water systems typically require water temperatures ranging from 50 to 90 degrees Celsius to be effective.
The use of heat pumps in this context is crucial, as they can achieve these temperature requirements more efficiently than traditional heating methods. The average COP for heat pumps is between 3 and 5, meaning they can produce three to five times as much heat as the electricity they consume. This is significantly higher than the efficiency of traditional steam boilers, which can vary widely but typically operate with efficiencies of 70% to 90%. Advanced heat pumps can even achieve higher efficiencies and are particularly useful in settings where maintaining specific, high temperatures is necessary for effective cleaning.
Benefits and Disadvantages
Integrating alternative cleaning methods such as hot water or chemical cleaning offers significant environmental and economic benefits. The reduced reliance on fossil fuels and the high efficiency of heat pumps, especially those with a high COP, contribute to lower operational costs and a smaller carbon footprint. For instance, replacing a gas-fired boiler system with a high-COP heat pump can drastically reduce energy consumption and emissions, since heat pumps use electricity more efficiently to generate the same or even greater amount of heat.
However, transitioning to these technologies also presents challenges. The initial cost of installing high-performance heat pumps can be significant, though these costs are often offset by long-term savings in energy and maintenance. Additionally, ensuring the compatibility of new heating systems with existing infrastructure can require careful planning and investment.
These additions provide a more detailed analysis of the efficiency metrics and practical considerations involved in switching to alternative cleaning methods supported by heat pumps. If you’d like, I can update the document with these changes and provide a new download link.
Conclusion
Adopting alternative cleaning methods such as chemical and hot water cleaning can significantly reduce the environmental impact of industrial cleaning processes. Each method has distinct advantages and challenges, but when integrated with high-temperature heat pumps, they offer a promising reduction in carbon emissions and energy use. Future research should focus on optimising these technologies and expanding their application to ensure broader adoption in the industry.
Add comment
Comments